Joining Mesh Edges Together
To understand what MeshToNurb does, one must also understand the fundamental differences between a Mesh model and a NURBS surface model. Although both can represent a 3D object as a computer model, they do it in completely different ways. A mesh represents 3D surfaces as a series of discreet facets, much as pixels represent an image with a series of colored points. If the facets or pixels are small enough, the image appears “smooth”. Yet, if we zoom in enough, we can still see the “pixelization” or granularity and that the object is not locally smooth and continuous.
NURBS surfaces are mathematical representations of curves and surfaces. They are capable of representing complex free form surfaces that are inherently smooth, and they keep their smooth shape when editing. There is no pixelization or granularity as with a mesh. Thus they behave more like a real person’s face rather than a pixelized image of that same face. It is important to note here that NURBS can be easily converted to Meshes at any time, in the same way that you can easily take a digital image of a person’s face with a camera.
So, going from Meshes to NURBS is like trying to reconstruct a person’s face from a pixelized digital image - it is a much more difficult task, and there are no quick automatic methods. Mesh terminology used in this article. To repeat, meshes are faceted representations of 2D and 3D surfaces. Making advanced analytics work for machine learning. Individual mesh facets in Rhino can have either 3 sides (triangles) or 4 sides (quads). They are represented on your computer screen as a series of connected lines in wireframe mode; in shaded modes each facet is given a “surface” for visualization purposes.
The points at the corners of the facets are called vertices. A series of facets join together to make a mesh object.
Important note: Although mesh facets are often believed to be always planar, this is an incorrect assumption. Only triangle meshes are guaranteed to have all planar facets. Quad facets may be planar, but they are not guaranteed to be so, as 4 non-coplanar points in space will describe a warped area.
NURBS terminology used in this article. There is a huge amount of information available on NURBS. It is a very complex subject and will not be discussed in detail in this article.

NURBS are curves based on mathematics. NURBS surfaces are generated by a series of NURBS curves in two directions (called “U” and “V”) interpolated to create a surface. We will consider only the simplest case of NURBS surfaces here – the so called “bilinear” surfaces defined by degree 1 NURBS curves (i.e. Lines) in both directions, as those are what are produced by MeshToNurb. When all the edges of the NURBS surface correspond with the original curves that generated the surface (the “natural” edges), the surface is called untrimmed. If the surface has been cut with a curve that is other than its natural edge, it is called trimmed. OK, so much for all the technogeekspeak.
As stated above, MeshToNurb does not automatically “reverse-engineer” mesh objects and make them into smooth surfaced NURBS objects. Sorry, no one-click miracles here. Once a 3D model is in mesh form, it's hard to recreate a smooth NURBS object from it. There is much info available on the subject of reverse engineering and its difficulties;. There are also several specialized reverse engineering software packages to partially automate this process.
They range from moderately expensive to very expensive. There are even a couple of plug-ins available to add this capacity to Rhino (but they are not free). What it does.
Mesh Quads are converted to 4-sided untrimmed degree1 NURBS surfaces. Again, “untrimmed” means the “natural” edges of the surface are the same as the outer boundaries and nothing has been “trimmed” off. Thus, the defining edges of the NURBS surface in this case are the same as the lines representing the Mesh face's edges. This implies two things: If the original mesh quad face was defined by 4 coplanar points, all the edge lines are in the same plane, and the resulting NURBS surface will be planar. If the quad face’s 4 mesh vertices are not co-planar, the edge lines of the NURBS surface will not be co-planar and the surface will be warped. This type of surface can also be called a “ruled surface”. Mesh Triangles.
Triangles are by definition planar. MeshToNurb will convert mesh triangles into either trimmed planar NURBS surfaces, or untrimmed planar NURBS surfaces with a singularity (one edge collapsed to a point), depending on whether you have set the command line option TrimTriangularFaces to Yes or No. That option is only available if you do not preselect the meshes before starting the command. The trimmed NURBS surface will be a degree 1 x 1 surface as with the quads, just with one half trimmed off to form a triangle. Based on the above, the resulting polysurface from MeshToNurb will have exactly the same edges as the original mesh model and be composed entirely of degree 1 x 1 (bilinear) NURBS surfaces. Triangle surfaces will be planar and trimmed or not according to the option chosen; quad surfaces will be untrimmed and either planar or not according to the planarity of their 4 corner points. Important note: MeshToNurb will not subdivide the quad areas into triangles to create planar surfaces.
Things to watch for. Mesh objects can contain from a few to hundreds to thousands to millions of polygons.
The mesh format is very compact for storing this faceted data. NURBS surfaces are much less compact in their definition.
A NURBS representation of a mesh object produced by MeshToNurb may easily take up 100 times as much data as the mesh does. Executing MeshToNurb on complex meshes composed of many thousands of triangles may run your computer out of memory and will produce very large file sizes.
If you have a recent machine with a good processor, enough memory, and a 64-bit operating system, this presents less of a problem. Downstream operations.
An understanding of the type of geometry produced is essential. As stated above, quad mesh facets are not guaranteed to be planar, and the quad NURBS results from MeshToNurb may be warped. They may not be developable without stretching. If you are using UnrollSrf on the NURBS polysurface, the results may be distorted or incorrect. To ensure planarity and correct unrolling, either triangulate the mesh before running MeshToNurb or check the mesh to see if all faces are planar.
(A script will be necessary to do this. There is no native Rhino tool currently available.) With all its limitations what is this command useful for then?
By hand or power? With a spring joint or not? Lang, Glen D. Huey & Christopher Schwarz pgs. 40-43 From the April 2009 issue #175 One of the most important joints in woodworking is the edge joint. Without it, our projects would look like they had been built from narrow popsicle sticks.
The joint bewilders many amateur woodworkers – perhaps because there are so many ways to go about it. Which method is best? Which tools are best? The senior staff of Popular Woodworking rarely agrees on anything (except the pizza place at which we sometimes eat lunch). And making edge joints is no exception. We do, however, agree on one principle when it comes to edge joints: You aren’t going to get consistent results by making your edge joints with a table saw blade. During the last decade or so we have tested a dozen table saw blades that claim to give you rips that are clean enough for an edge joint.
People Joining Together
Perhaps that is true if your work is on a job site, if you are working in easy-to-compress softwoods, or if you are a fanatic about keeping your saw exquisitely tuned. But we have not found these saw blades to give us results that are 100 percent satisfactory.
And so we look to other tools and machines to create edge joints that result in seamless seams and maximum glue adhesion. Understanding History This joint has always made woodworkers edgy (sorry).
Early written accounts of making edge joints would tout a variety of approaches as the best to ensure the finished panel stayed together. Some accounts recommended loose splines. Some recommended using a tongue-and-groove joint.
There was even a special kind of nail that could be used for joining edges. More modern methods of reinforcement include dowels, biscuits, Festool Dominos and pocket screws.
However, we contend that if you have two surfaces that will mate perfectly then you don’t need additional reinforcement. A well-made glue joint is stronger than the wood surrounding it.
Another area of confusion: Other early accounts recommend using a “spring joint” when gluing up a panel. A spring joint is when the edge joint has a small gap (only a few thousandths of an inch) in the middle of the seam.
When you clamp across the middle of the panel, it closes the entire seam. The advantage of a spring joint is that you use fewer clamps to make your panels. Also, if your stock is a little wet, a spring joint can keep the ends tightly together as the stock dries out (end grain loses moisture much more rapidly than face grain). Some opponents of spring joints say that the gap introduces some stress into the panel that could (in time) cause the joint to open. Other opponents say that spring joints are simply a waste of good shop time. In our shop, the opinion is divided.
Publisher Steve Shanesy and Senior Editor Robert W. Lang don’t use spring joints. And so we’re going to show Lang’s approach, which uses a powered jointer without any special setups to introduce a spring joint. Senior Editor Glen D. Huey likes spring joints as a way to reduce the number of clamps he needs to use. He figured out a fairly simple jointer setup and hand trick that makes spring joints an easy thing to do on the powered jointer.
And then there’s me. I like spring joints and I like making them using handplanes. And so I’m going to show you how to make an edge joint using historical methods I’ve dug up from the old books. So step away from your table saw for a moment and take a look at these three time-tested techniques and decide which one would be best for you. — Christopher Schwarz Jointer – No Spring Joint My approach to edge joining comes from my training in production shops, and my philosophy that a joint under tension increases the chances of failure in the future. I don’t use a spring joint, and I run edges over a well-tuned jointer just before gluing. There isn’t anything romantic or inspiring about my approach, but it works well, and it doesn’t take long.
I’m a bit persnickety about machine set-ups, and I get cranky if I have to remember what area of a machine is off a little, and in what direction that offset is. In truth, I have trouble remembering things like that, so it’s easier to have the jointer knives even with the outfeed table and the fence square. I select wood for panels and tabletops based on appearance. You can’t convince me that there is an advantage to alternating growth rings, or arranging the boards so they will be easy to plane later on.
The goal is to make a pieced-together board look like it grew that way. If the material is prepared correctly I don’t worry about it warping, and if I need to fuss a little when doing the final smoothing, that’s OK. This is an area where mastery of the fundamentals is the key to success. Dead-flat boards with straight and square edges are easy to put together. Glue them together on a flat surface and it can actually be an enjoyable, relaxing experience. If the boards are straight and the thickness consistent before gluing, there is little to be done afterwards.
I crosscut the rough lumber to about the size I need, but when I surface, edge and rip I’m thinking WAP and TAP – “wide as possible” and “thick as possible.” This leaves some margin for me to work around defects or ugly spots without starting over. I try to keep parts from a single board together to make it easier to match color and figure. There may have been a time when a spring joint made sense, especially if the moisture content of the wood was too high.
Hands Joining Together
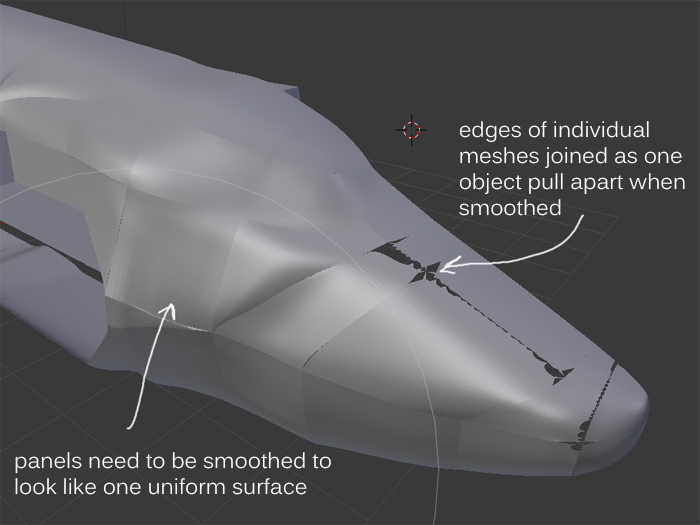
In this day and age, it makes as much sense as collar stays and celluloid dickies. The finished glue line is nearly invisible. After letting the glue dry for an hour, the clamps can be removed. Complete curing takes longer, so I let the assembly dry overnight before further surfacing. If I do it right, it only takes a few swipes with a card scraper to clean up the panel. Jointer – With Spring Joint I prepare my edges with a jointer, but I also like a small spring in my joint.
Because I’m not a handplane aficionado, I turn to a machine. As a result, I have to bend the rules. In most articles on setting jointer knives you’re instructed to use a dial indicator to set the knives perfectly level and in line to the outfeed table. While you do need to set the knives level to one another, alignment with the outfeed table is optional. I set my knives so there is.030″ of slope over the 8″ blade.
The end of the knives closest to the operator are below the outfeed table by.015″. At the back they are.015″ above the outfeed table.
With the knives below the outfeed table, you’ll get a taper if you transfer hand pressure to the outfeed table as soon as there is ample surface to do so. That’s another rule I choose not to follow given my blade arrangement! When edge jointing, I keep my downward-pressure hand at the center of the board. As the board runs over the knives it climbs slightly above the outfeed table. At the center of the board my pressure transfers to the outfeed table and the slight tapering effect completes the cut. Bingo, a spring joint.
And don’t worry about flatness when face jointing. Because a jointed face is not the final surface when milling for thickness, any small variations are erased at a planer. And if you’re worried about the small bevel on the edge of a 3⁄4″ board, you’re looking at less than a.003″ variation. Bottom line: I can dial in my spring joint by adjusting my fence position along the blades. When everything works as planned, I need only one clamp for most panel assemblies, but I generally use two.
(To see how this process works for faces and edges, go to popularwood working.com/video.) — GH. Keep it thin. The idea is to create a bow or spring in the board that allows the ends of the joint to be tight as the center gap is closed under clamp pressure. If you create a gap that’s too large, the pressure at the center of the board could become overly strong and cause stress at the glue line. And you don’t gain anything if the bow is too light. I find a sweet spot where a single sheet of paper slides while both ends are in contact with the jointer bed. Another test is to place no more than a playing card between two board edges as you dry-fit the panel.
Handplanes Though I first learned to prepare edge joints by machine on a powered jointer, I prefer to do it by hand whenever possible. When I’m working for myself and time isn’t a concern, I’ll use the pure hand-tool methods shown here. It’s a bit slower than the power-tool methods, but I enjoy it immensely. When every second counts, however, I’ll prepare my edges on a power jointer and then use a jointer plane to introduce the spring joint. You can mix and match the hand and power methods any way you see fit.
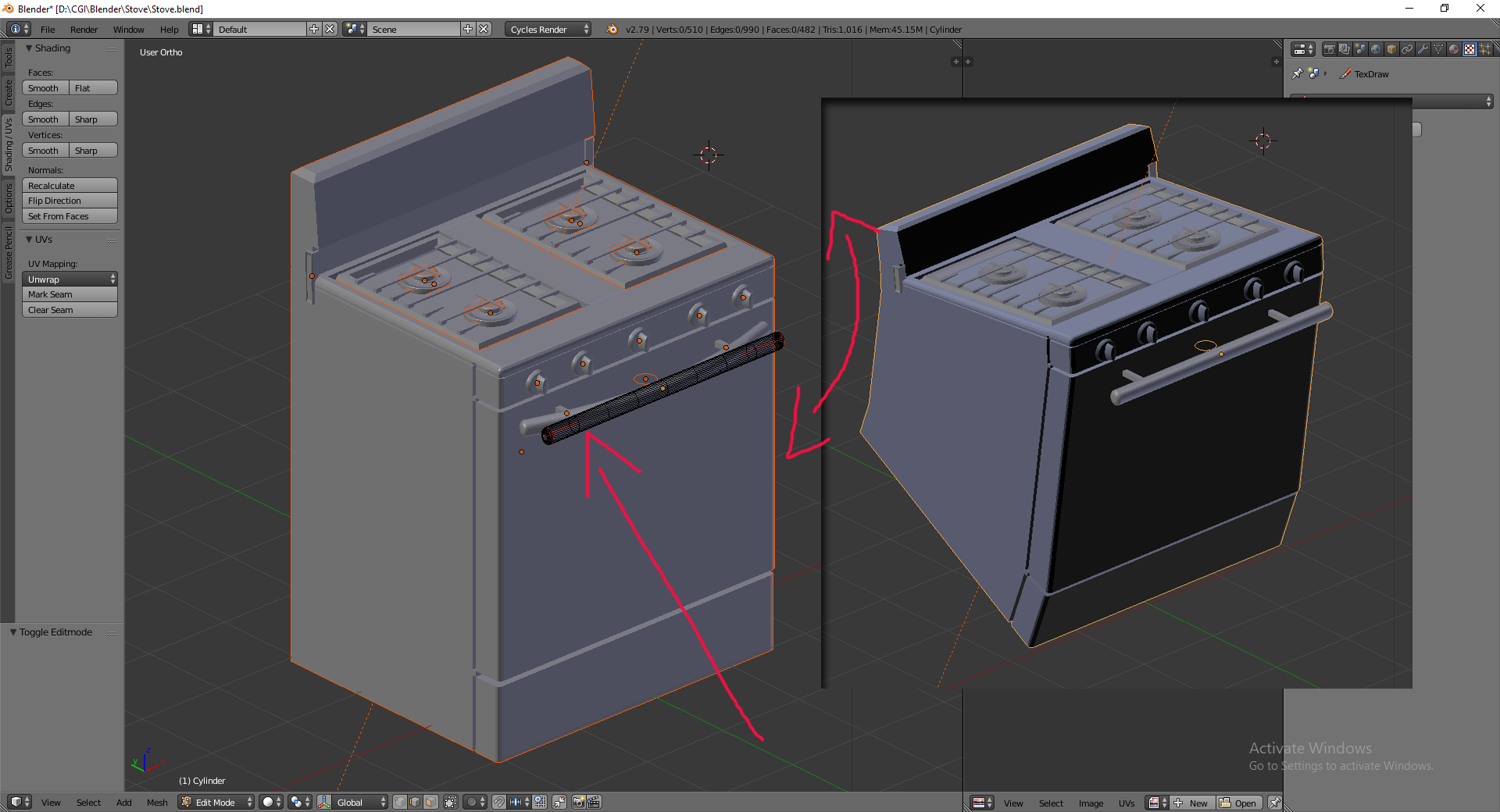
Here are a couple details and subtleties of my process. Though I use a scrub plane to dress my rough edges, you can also use a table saw, band saw, drawknife or a hatchet for the coarse removal of material. Also, the cutter in my jointer plane has a very subtle curve on its edge. This allows me to correct an out-of-square edge by shifting the plane left or right on the edge of the board. But the curve is not so pronounced that it produces a curved edge on the board.
The edge looks flat to a try square. You can read more about this process in the August 2005 issue (#149) of Popular Woodworking in an excellent article by David Charlesworth titled “Learning Curves.” And you can find it online at.